Manufacturing Lead Times
This chapter tells you everything you need to know about manufacturing lead times. This chapter covers the following topics:
- Overview of Lead Time Management
- Calculating Lead Times
For manufactured items, you can automatically compute manufacturing(processing) and cumulative lead times for a specific item or a range of items. You can also maintain this information manually. You must manually assign all lead time information for purchased items.
Note: You can calculate manufacturing and cumulative lead times for manufacturing or engineering items.
Updating the values assigned to your lead times may impact functions that use dynamic lead time offsetting- such as material and resource requirements planning. Updating cumulative lead times can also impact material plans and available to promise calculations if these lead times are used to set time fences.
Item Lead Time Attributes
For all scheduled time elements, which are less than the standard workday, the system will compute the lead time day by dividing the lead time element by 24. The standard workday is defined in the workday calendar. Oracle Manufacturing stores the following lead time information for each item:
1.2. Processing Lead Time: The time required to procure or manufacture an item. You can compute processing lead time for a manufactured item, or manually assign a value. Processing lead time is computed as the time as total integer days required to manufacture 1 lead time lot size of an item. You must manually assign a processing lead time for purchased items. Processing lead time does not include preprocessing and postprocessing lead times.
For Manufacturing item processing lead time = fixed lead time + (variable lead time * lead time lot size)
1.3. Post Processing Lead Time: A component of total lead time that represents the time to make a purchased item available in inventory from the time you receive it. Manually enter postprocessing lead time for each purchased item. Postprocessing lead time for manufactured items is not recognized.
2.1. Fixed Lead Time: The portion of manufacturing lead time that is independent of order quantity. You can enter this factor manually for an item, or compute it automatically for manufactured items.
2.2. Variable Lead Time: The portion of manufacturing lead time that is dependent on order quantity. You can enter this factor manually for an item, or compute it automatically for manufactured items.
2.3. **Total Lead Time**: The fixed lead time plus the variable lead time multiplied by the order quantity. The planning process uses the total lead time for an item in its scheduling logic to calculate order start dates from order due dates.
3.1. Cumulative Manufacturing Lead Time: The total time required to make an item if you had all raw materials in stock but had to make all subassemblies level by level. Oracle Bills of Material automatically calculates this value, or you can manually assign a value.
3.2. Cumulative Total Lead Time: The total time required to make an item if no inventory existed and you had to order all the raw materials and make all subassemblies level by level. Bills of Material automatically calculates this value, or you can manually assign a value.
3.3. Lead Time Lot Size: The quantity you use to calculate manufacturing lead times. You can specify an item's lead time lot size to be different from the standard lot size.
4. Dynamic Lead Time Offsetting: A scheduling method that quickly estimates the start date of an order, operation, or resource. Dynamic lead time offsetting schedules using the organization workday calendar.
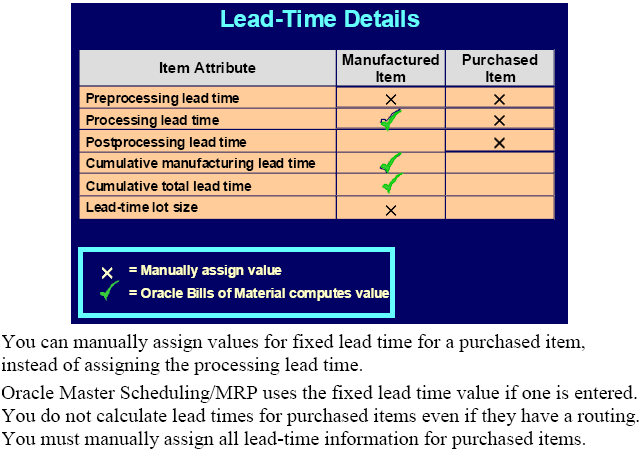
Imp Note
1. Oracle MRP/Master Scheduling considers preprocessing lead time when offsetting dates.
Oracle Bills of Material and Oracle Engineering do not consider preprocessing when computing manufacturing (processing) lead time.
2. Dynamic Manufacturing Lead Times (Fixed lead times, variable lead times and processing lead times) for manufacturing items are claulated by running the Manufacturing Lead Time GUI from Routing window.
Cumulative manf lead time and cumulative total lead times can be calculated by running Rollup cumulative lead times (Cumulative Lead Times for Report Set) request either from bill/Routing window.
Am i correct in lead time calcualtion
For manufacturing items the lead time depends on
i> Lead of each component
ii>Lead Time Percent
Oracle Manufacturing stores the lead time percent for each routing operation as the percent of manufacturing (processing) lead time required for previous operations, calculated from the start of a job to the start of an operation. For example, if an item's manufacturing lead time is two days and the primary routing has two operations with the same duration (1 day), the first operation's lead time percent is zero and the second operation's lead time percent is 50%.
iii>Offset Percent
Oracle Manufacturing stores the offset percent for each resource on a routing operation as the percent of manufacturing (processing) lead time required for previous operations, calculated from the start of the job to the start time of a resource at an operation. For example, both operations in the previous example for lead time percent require one day (eight hours) to perform. If you have two different resources assigned to the second operation, and each resource requires four hours to complete their task, the offset percent is 50% for the first resource and 75% for the second resource.